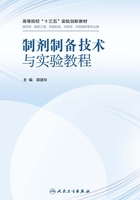
上QQ阅读APP看书,第一时间看更新
第四章 固体制剂制备共性技术
第一节 粉 碎 技 术
一、概述
粉碎的定义是指是将大块物料借助机械力破碎成适宜大小的颗粒或细粉的操作。粉碎的主要目的在于减小粒径,增加比表面积。对于固体制剂来说粉碎过程具有如下意义:①有利于混合时各成分分布均匀;②有利于提高难溶性药物的溶出速度以及生物利用度;③有利于提高固体药物在液体、半固体、气体中的分散度。显然,粉碎对药品质量的影响很大,但必须注意粉碎过程可能带来的负面作用,如晶型转变、热分解、黏附与团聚性的增大、堆密度的减小、在粉末表面吸附的空气对润湿性的影响、粉尘飞扬、爆炸等。
(一)物料的物理性质
1.硬度
物料的坚硬程度,如以莫式硬度表示,从软到硬为别为1~10。滑石粉为1,金刚石为10,软质物料为1~3,中等物质为4~6,硬质物料为7~10。制药过程需要粉碎的料中,大多数为硬度1~3的软质物料。
2.脆性
脆性指的是物料受到外力冲击后易于碎裂成细小颗粒的性质。制药过程中的晶体物料容易沿结合面碎裂成小晶体,易于粉碎;非极性晶体物料由于受力时会产生变形从而阻碍粉碎过程,通常可加入少量液体渗入固体分子间隙以降低分子间的内聚力。
3.弹性
固体受力后发生变形,撤去力后恢复原有状态的能力。显然,弹性是不利于粉碎的,对于一些非晶体、有一定弹性的药物,可采取降低温度的方法,减小弹性变形,增加脆性以有利于粉碎。
4.水分
一般来说,物料所含水分越少越容易粉碎,但水分过少容易引起粉尘飞扬,故常控制水分含量为3.3%~4%进行粉碎为宜。
5.温度
粉碎过程中,部分机械能会转换成热能,造成被粉碎物料分解、变软、变黏,影响粉碎过程的进行,这时,需要采用低温粉碎来解决。
6.重聚性
粉碎会引起表面能增加,形成不稳定状态。这时表面能由于有趋于稳定的特性而引起的粉末重新聚集的现象称为重聚性,可通过混合粉碎阻止重聚现象发生。
(二)粉碎机理
物质的形成依赖于分子间的内聚力,粉碎过程主要是依靠外加机械力的作用破坏物质分子间的内聚力来实现的。被粉碎的物料受到外力的作用后在局部产生很大应力或形变。开始表现为弹性变形,当施加应力超过物质的屈服应力时物料发生塑性变形,当应力超过物料本身的分子间力时即可产生裂隙并发展成为裂缝,最后则破碎或开裂。
(三)粉碎方式
根据粉碎设备和粉碎部位的不同,粉碎过程中打破分子内聚力的常用的外加力有:冲击力、压缩力、剪切力、弯曲力、研磨力等。被处理物料的性质、粉碎程度不同,所需施加的外力也有所不同。冲击、压碎和研磨作用对脆性物质有效;纤维状物料用剪切方法更有效;粗碎以冲击力和压缩力为主,细碎以剪切力、研磨力为主;要求粉碎产物能产生自由流动时,用研磨法较好。实际上多数粉碎过程是上述的几种力综合作用的结果。
(四)粉碎方法
1.开路粉碎
物料仅通过一次粉碎就得到粉碎产品的操作称为开路粉碎,开路粉碎适合粗碎或者进一步粉碎的预粉碎。
2.循环粉碎
粉碎产品中如有未达到要求粒径的大颗粒,通过筛分设备将其分离出来再返回粉碎设备继续粉碎的方法称为循环粉碎。循环粉碎适用于细碎或者粒度范围要求较严格的粉碎。
3.干法粉碎
将物料经过适当的干燥处理,使物料中的水分含量降低至一定程度再进行粉碎的方法。含水量多少应由所选粉碎设备确定,如采用球磨机,含水量应在5%以下,万能粉碎机则应该控制在10%左右。
4.湿法粉碎
在粉碎过程中加入适当液体的粉碎方法,又称为加液研磨。液体的作用有两个,一是渗入固体物料组织间隙减小分子间引力,二是防止粉碎过程中粉尘飞扬及粒子凝聚。湿法粉碎适用于有毒、刺激性,以及要求较细颗粒的物料。但是注意,选用湿法粉碎的物料应当以遇湿不膨胀、化学性质不变化为原则。用于湿法粉碎的液体通常为乙醇或水。
5.单独粉碎
指将一味药料单独进行粉碎处理。单独粉碎既可以按物料性质选取合适设备,又可避免粉碎时因不同物料损耗不同而引起的含量不准确现象。需要进行单独粉碎的药料有氧化性药物与还原性药物(分别粉碎,防止反应剧烈发生爆炸)、贵重细料药物(牛黄、珍珠等,以利于管理并可减少损失)、某些需特殊处理的粗料药(如在冬春季节粉碎,利用低温增强其脆性的乳香、没药)。
6.混合粉碎
指将数味药料掺和进行粉碎。若处方中某些药物的性质及硬度相似,则可以将它们掺和在一起粉碎,这样既可避免一些黏性、油性药物单独粉碎的困难,又可将粉碎与混合操作同时进行。如常将熟地黄、麦冬、黑芝麻、杏仁、核桃仁等黏软、油性大的药物与其他药物粗末混合后粉碎,使其他药物吸收黏性和油性成分,以利粉碎和过筛。
7.低温粉碎
低温粉碎是指将冷却到脆化点温度的物质在外力作用下破碎成粒径较小的颗粒或粉体的过程。采用低温粉碎,不但产品的粒度较细,能够较好的保持药物的有效成分,还可以降低粉碎机械能的消耗。低温粉碎适用于具有热塑性、强韧性、热敏性、挥发性及熔点低的药材。需要注意的是,低温粉碎后的药材需置于防潮容器内,避免长时间暴露于空气中受潮。
8.超微粉碎
将物料进行细胞级别的粉碎,粉碎后粒径可达到5微米左右,植物细胞的破壁率达到95%,大大提高丸剂、散剂等含有原药粉末制剂的生物利用度,有效成分直接暴露,使药物起效更加迅速。
9.纳米粉碎
纳米粒子大小一般在1~100纳米之间,药材经过纳米粉碎后,植物药材中细胞结构均被破坏,使细胞内不溶物、树脂、黏液质溶出,药材经纳米粉碎后化学性质发生相应变化,对制剂的影响还有待进一步研究。
(五)粉碎能量
1.粉碎度
物料粉碎前的粒度 D 1与粉碎后的粒度 D 2之比称为粉碎度或粉碎比。
按照 n的大小,粉碎的等级可分为粗碎、中碎、细碎、超细碎四个。粗碎的 n=3~7,物料粉碎后的直径 D 2在数毫米至数十毫米之间;中碎 n=20~60, D 2在数百微米至数毫米之间;细碎 n>100, D 2在数十微米至数百微米之间;超细碎 n=200~1000, D 2在数微米至数十微米之间;
2.粉碎过程的能量消耗
一般情况下,在粉碎过程中所需的能量消耗于粒子的变形、粒子破碎时新增的表面能、粉碎室内粒子的移动、粒子间以及粒子与粉碎室间的摩擦、振动与噪音、设备转动等。研究结果表明,粉碎操作的能量利用率非常低,消耗于产生新表面的能量在总消耗能量中只占0.1%~1%,因此如何提高粉碎的有效能量是粉碎操作研究的主攻方向之一。随着粉碎过程的不断进行,即物料的粒径越小,达到一定粉碎度所需能量越大,越不易粉碎。粉碎过程受物料的物性、形状、大小、设备、作用力、操作方式等复杂条件的影响,很难用精确的计算公式来描述能量的消耗。科学家们曾提出过不少经验理论与计算公式,本节介绍其中著名的三个能量学说。
雷廷格(Rittingger)定律认为:粉碎所需的能量与表面积的增加成正比,该定律适用于数十微米到数百微米粒度范围的细粉碎中,因为细碎中表面积的增加比较显著。而且适用于脆弱的物料的粉碎。
基克(Kick)定律认为:粉碎所需的能量与粒子体积的减少成正比,该定律适用于数十微米到数毫米粒度范围的粗碎中,因为粗碎时体积的变化较为显著。此时的能量消耗只与粉碎比( D 1/ D 2)有关,与粒径大小无关。
朋特(Bond)定律认为:粉碎所需的能量与颗粒中裂缝的长度成正比,或者说粉碎所需的能量与粒径的平方根成反比。该理论介雷廷格于学说与基克学说之间。
为了评价物料粉碎的难易程度,提出了功指数的概念。功指数是将无穷大( D 1=∞)的粒子粉碎成 D 2=100µm时所需的能量,功指数小的物料可碎性或可磨性较好。功指数也是衡量粉碎操作效率的最有用方法之一。
对整个粉碎过程来讲,开始阶段由于体积的减少更为显著而遵循基克定律,而最终阶段的细粉碎过程中表面积的增加更为突出而遵循雷廷格定律,粉碎的中间阶段遵循朋特定律。
二、常用设备及注意问题
1.研钵
实验室中研碎实验材料的容器,配有钵杵。用于研磨固体物质或进行粉末状固体的混合。其规格用口径的大小表示。常用的为瓷制品,也有由玻璃、铁、玛瑙、氧化铝材料制成的研钵。进行研磨操作时,研钵应放在不易滑动的物体上,研杵应保持垂直。大块的固体只能先压碎再研磨,不能用研杵直接捣碎,否则会损坏研钵、研杵或将固体溅出。研磨对皮肤有腐蚀性的物质时,应在研钵上盖上厚纸片或塑料片,然后在其中央开孔,插入研杵后再行研磨,研钵中盛放固体的量不得超过其容积的1/3。研钵不能进行加热,洗涤研钵时,应先用水冲洗,耐酸腐蚀的研钵可用稀盐酸洗涤。研钵上附着难洗涤的物质时,可向其中放入少量食盐,研磨后再进行洗涤。该设备同时适用于干、湿法粉碎。
2.球磨机
将不锈钢或陶瓷制成的圆柱筒内装入一定数量不同大小的钢球或瓷球构成。使用时将药物装入圆筒内密盖后,用电动机转动。当圆筒转动时,带动钢球(或瓷球)转动,并带到一定高度,然后在重力作用下抛落下来,球的反复上下运动使药物受到强烈的撞击和研磨,从而被粉碎。粉碎效果与圆筒的转速、球与物料的装量、球的大小与重量等有关。圆筒转速过小时,球随罐体上升至一定高度后往下滑落,这时物料的粉碎主要靠研磨作用,效果较差。转速过大时,球与物料靠离心力作用随罐体旋转,失去物料与球体的相对运动。当转速适宜时,除一小部分球下落外大部分球随罐体上升至一定高度,并在重力与惯性力作用下沿抛物线抛落,此时物料的粉碎主要靠冲击和研磨的联合作用,粉碎效果最好。可见圆筒的转速对药物的粉碎影响较大。临界转速是使球体在离心力的作用下开始随圆筒做旋转运动的速度。
根据物料的粉碎程度选择适宜大小的球体,一般来说球体的直径越小、密度越大,粉碎的粒径越小,适合于物料的微粉碎,甚至可达纳米级粉碎。一般球和粉碎物料的总装量为罐体总容积的50%~60%。
球磨机是最普通的粉碎机之一,有100多年的历史。球磨机的结构和粉碎机理比较简单。该法粉碎效率较低,粉碎时间较长,但由于密闭操作,适合于贵重物料的粉碎、无菌粉碎、干法粉碎、湿法粉碎、间歇粉碎,必要时可充入惰性气体,所以适应范围很广。
3.万能粉碎机
万能粉碎机对物料的作用力以冲击力为主,适用于脆性、韧性物料以及中碎、细碎、超细碎等,应用广泛。其典型的粉碎结构有锤击式和冲击柱式。锤击式粉碎机的结构有高速旋转的旋转轴,轴上安装有数个锤头,机壳上装有衬板,下部装有筛板。当物料从加料斗进入到粉碎室时,由高速旋转的锤头的冲击和剪切作用以及被抛向衬板的撞击等作用而被粉碎,细粒通过筛板出料,粗粒继续在机内被粉碎。粉碎粒度可由锤头的形状、大小、转速以及筛网的目数来调节。冲击柱式粉碎机(也叫转盘式粉碎机),在高速旋转的转盘上固定有若干圈冲击柱,另一与转盘相对应的固定盖上也固定有若干圈冲击柱。物料由加料斗加入,由固定板中心轴向进入粉碎机,由于离心作用从中心部位被甩向外壁的过程中受到冲击柱的冲击,而且冲击力越来越大(因为转盘外圈线速大于内圈线速),最后物料达到转盘外壁环状空间,细粒由底部的筛孔出料,粗粒在机内重复粉碎。粉碎程度与盘上固定的冲击柱的排列方式有关。
4.流能磨
亦称气流粉碎机,其粉碎机理完全不同于其他粉碎机,物料被压缩空气引射进入粉碎室,7~10个气压的压缩空气通过喷嘴沿切线进入粉碎室时产生超音速气流,物料被气流带入粉碎室被气流分散、加速,并在粒子与粒子间、粒子与器壁间发生强烈撞击、冲击、研磨而得到粉碎。压缩空气夹带的细粉由出料口进入旋风分离器或袋滤器进行分离,较大颗粒由于离心力的作用沿器壁外侧重新带入粉碎室,重复粉碎过程。粉碎程度与喷嘴的个数和角度、粉碎室的几何形状、气流的压缩压力以及进料量等有关。一般进料量越多,所获得粉碎物的粒度越大。气流粉碎机的粉碎有以下特点:①可进行粒度要求为3~20µm超微粉碎,因而具有“微粉机”之称;②由于高压空气从喷嘴喷出时产生焦耳—汤姆逊冷却效应,故适用于热敏性物料和低熔点物料的粉碎;③设备简单、易于对机器及压缩空气进行无菌处理,可用于无菌粉末的粉碎;④和其他粉碎机相比粉碎费用高,但粉碎粒度的要求较高时还是值得的。
5.颚式破碎机
颚式破碎机是一种构造简单,工作可靠,维修方便的破碎机械,它广泛地用于各种块状硬质物料的粗碎和中碎。加入到颚式破碎机破碎腔(由固定颚板和活动颚板组成的固定空间)中的物料,由于活动颚板作周期性的往复运动。当活动颚板靠近固定颚板时,物料受到挤压和劈裂作用而破碎。当活动颚板离开固定颚板时,已被粉碎到小于排料口的物料,靠自重从排料口排出。位于破碎腔上还未完全破碎的物料,也随之落到破碎腔下部,再次受到颚板的挤压作用而破碎。
6.胶体磨
由电动机通过皮带传动带动转齿(或称为转子)与相配的定齿(或称为定子)作相对的高速旋转,其中一个高速旋转,另一个静止,被加工物料通过本身的重量或外部压力(可由泵产生)加压产生向下的螺旋冲击力,透过定、转齿之间的间隙(间隙可调)时受到强大的剪切力、摩擦力、高频振动、高速旋涡等物理作用,使物料被有效地乳化、分散、均质和粉碎,达到物料超细粉碎及乳化的效果。胶体磨首先是一种离心式设备,它的优点是结构简单,设备保养维护方便,适用于较高黏度物料以及较大颗粒的物料。它的主要缺点也是由其结构决定的。首先,由于作离心运动,其流量是不恒定的,对于不同黏性的物料其流量变化很大。举例来说,同样的设备,在处理黏稠的油漆类物料和稀薄的乳类流体时,流量可相差10倍以上;其次,由于转定子和物料间高速摩擦,故易产生较大的热量,使被处理物料变性;第三,表面较易磨损,而磨损后,细化效果会显著下降。
7.搅拌磨
利用搅拌装置使研磨介质运动而产生冲击、剪切、研磨作用,从而粉碎物料的设备。常规磨机是靠筒体运动带动研磨介质运动,搅拌磨机输入的功率直接用于搅拌机构的旋转,使研磨介质运动而粉碎物料,故其能量效率高于常规磨机和振动磨机。搅拌磨机可以间歇或连续生产。根据筒体形状可分为槽型、环型、立式等类型。
8.切药机
稳定性好,精密度高,易于操作,切片连续均匀。适用于根、茎、叶、草等切制,能将药用部位切成段、片、条或碎块。