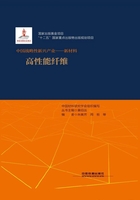
2.4 发展碳纤维产业背景及战略意义
2.4.1 碳纤维在国民经济和国防建设重大工程和项目中的地位和作用
碳纤维是国民经济和国防建设不可或缺的一种性能优异、应用广泛的战略性新材料,具有碳材料的各种优越性能和纤维材料的柔软可加工性,是先进复合材料最重要的增强体,广泛应用于航空航天、风力发电、汽车制造、建筑工程、体育休闲等领域。在航空航天方面,碳纤维增强复合材料可有效减小飞机质量,节省燃油,降低制造成本,增大航程。目前碳纤维增强复合材料在小型商务飞机和直升机上的使用量已占70%~80%,在军用飞机上的使用量占30%~40%,在大型客机上的使用量占15%~50%[65]。2010年我国全面启动和实施大飞机重大专项整体配套项目,2015年11月国产大飞机C919完成总装,其中碳纤维复合材料的用量仅为12%,不足最新民航飞机碳纤维用量的1/4,未来对碳纤维的需求仍有较大的空间。在风力发电方面,使用碳纤维可有效减小发电机组叶片的质量,同时增加叶片的强度和韧性,提高发电功率。预计2020年中国市场将需要超过2.5万台大容量风机,对碳纤维有较大的需求量。在汽车制造领域,汽车中的传动轴、顶篷、保险杠、车体和底盘均可使用碳纤维增强复合材料[66]。通过将碳纤维增强复合材料替代金属材料可有效减小汽车质量,降低能源消耗。美国复合材料协会(ACMA)在2012年指出,如果碳纤维的价格降为现在的一半,在2017年仅汽车领域全球对碳纤维的需求即可达13.8万t,市场前景广阔。在建筑工程方面,碳纤维可用于加固修复混凝土结构,提高结构构件的力学性能,解决钢筋生锈、老化而带来的问题以及地震等自然灾害带来的危害,延长建筑物使用寿命。随着碳纤维价格的降低,碳纤维在建筑工程方面的应用量将逐渐增加。在体育休闲方面,碳纤维已广泛应用于自行车、球拍、渔具等方面,2014年我国碳纤维在体育休闲方面的用量已达6100t,占所有应用领域的58%。此外,碳纤维在压力容器、船舶、电缆等其他方面也有着重要的应用。
图2-8所示为近几年全球碳纤维需求趋势图[67]。2008年全球对碳纤维的需求量仅为36.4kt,而2014年的需求量则达到53.5kt,每年的平均增长率在6%~8%之间。近两年对碳纤维的需求量更是呈现出较大的增幅,2016年的需求量达到76.5kt,预计2020年全球对碳纤维的需求量将达到112.0kt。表2-1所示为2016年全球碳纤维的需求领域及相应的需求量[67],其中航空航天领域的需求量达17.6kt,为总需求量的23%,对应的经济效益为1056.0百万美元,占总经济效益的50%,排名第一。航空航天领域碳纤维用量的提高主要是由于波音787、空客A350及A380等飞机的生产,碳纤维复合材料在整个飞机质量中占的比例提高,用量相应得到提高。风电叶片领域碳纤维的用量占据总用量的23.5%,成为碳纤维的第二大应用领域。此外,2016年碳纤维在体育休闲、汽车制造和混配模成形领域的需求量也较大,分别达到12.0kt、9.1kt和8.8kt。

图2-8 全球碳纤维需求趋势图(加*为预测数据)
表2-1 2016年全球碳纤维的需求领域及相应需求量

图2-9所示为我国近几年碳纤维需求趋势图[67]。2008年我国碳纤维的需求量为8.2kt,2015年的需求量达到16.8kt,增长幅度不大,但每年均平稳增长。随着我国航空航天事业的发展以及大飞机项目的开展,碳纤维的需求量将在2016—2020年间迅速提升,预计到2020年可达到30.8kt。图2-10所示为2016年我国碳纤维的主要应用领域及用量[67]。由图可知,体育休闲类占据了碳纤维用量的较大比例,为48%,其次为风电叶片和建筑补强,分别占碳纤维总用量的15%和8%。而航空航天领域的用量为400t,仅占总用量的2%。对比全球碳纤维在航空航天领域占的比例(23%),可以发现我国在此领域要远远落后,其原因一方面是由于国产大规模生产的碳纤维强度还达不到航空航天的要求,另一方面是由于军工碳纤维领域要求严格,门槛高,认证周期长,限制了碳纤维在航空航天领域的应用。此外,2016年我国碳纤维在汽车领域的需求量仅为300t,占总需求量的2%,用量提升空间巨大。

图2-9 中国碳纤维需求趋势图(加*为预测数据)

图2-10 2016年我国碳纤维的主要应用领域及用量
综上,碳纤维在国民经济和国防建设中具有不可或缺的地位,其涉及面广、辐射带动能力强,加快碳纤维的发展,提高碳纤维用量,对推动传统材料升级换代、满足国家重点工程迫切需求、争夺未来国际竞争优势具有重大意义。
2.4.2 国外碳纤维产业发展现状及趋势
2016年全球碳纤维市场产能总计约为13.9万t,其主要生产地是日本、欧洲和美国。表2-2所示为2016年全球碳纤维理论产能排名前十的企业[67]。由表中数据可知,日本东丽公司和美国卓尔泰克公司成为碳纤维的主要供应商。2013年东丽公司开始收购卓尔泰克公司,2014年完成收购,一举成为世界顶级碳纤维企业。东丽公司以生产小丝束碳纤维为主,其性能优异,多用于航空航天等领域。美国卓尔泰克公司主要生产大丝束碳纤维,力学性能较低,作为通用级别纤维主要应用在民用领域和一般的工业中,其制备原料为民用PAN原丝,因此,相对小丝束碳纤维而言,属于成本较低的生产技术。
表2-2 2016年全球碳纤维理论产能排名前十的企业

东丽公司通过控制PAN原丝和碳纤维的结构缺陷,优化PAN纤维的截面设计,成功开发出以往技术所不能达到的更高强高模碳纤维T1100,其价格比以往的T1000G还要低[68]。2014年3月东丽公司利用碳化技术,在纳米尺度上精确控制纤维结构,成功开发出兼具高拉伸强度和高拉伸模量的T1100G碳纤维。目前东丽与美国波音公司已签订合同,自2014年起连续十年为波音公司供应碳纤维,此订单金额超过1万亿日元,创两家公司交易额的历史新高,主要为向波音公司的现有机型和下一代大型客机777X的主机翼部分供货。为完成订单,东丽公司计划投资1千亿日元,在美国建设世界最大规模的碳纤维工厂。此外,由于欧洲空客公司的大量订单,东丽公司计划提高用于飞机等轻质化所需PAN基碳纤维的产能,同时不断改进生产工艺和降低成本,使其在汽车用碳纤维方面也争取达到领先水平[68]。
德国西格里公司与宝马集团、三星集团等集团合作,进一步扩大了其碳纤维的产量,2016年其碳纤维产能达到15.0kt,排在第三位。三菱公司2016年碳纤维的产能为12.1kt,成为第四大碳纤维供应公司。其指出全球碳纤维需求年均增速将超过20%,特别是可再生能源和提高燃料效率的汽车轻量化解决方案正推动碳纤维应用快速增长。为适应压缩天然气瓶、汽车、压力容器、风力发电等领域对碳纤维的大量需求,公司已着手扩大位于美国的碳纤维生产能力,计划于2017年收购德国SGL集团在美运作的一个碳纤维厂,预计增加1000t年产能。此外,东邦公司2016年碳纤维的产能为11.5kt,排在第五位,其PAN基碳纤维已取得新一代中型民航客机A350的认证,目前正计划增加日、德PAN基碳纤维的生产线,同时对美国的部分生产线进行改造和技术升级,扩大了预浸料和成形品的比例。
表2-3所示为PAN基碳纤维发展的主要历程,其发展过程可大致分为四个阶段[69]。由表2-3可发现,PAN基碳纤维经历了“从无到有”“从弱到强”的过程。进一步提升碳纤维的强度和模量成为未来碳纤维的发展方向。根据分子间结合力模拟可得到碳纤维的理论抗拉强度高达180GPa,拉伸模量高达1020GPa,而目前碳纤维的最高抗拉强度仅为理论值的5%,提升空间巨大。尽管碳纤维的拉伸模量已接近理论目标,但生产兼具高强度和高模量的碳纤维难度较大,有待进一步的攻克。碳纤维的普及成为其第二大发展方向。进一步提高大丝束碳纤维的产量,降低其生产成本,拓展其在民用市场中的应用成为急需解决的问题。碳纤维的第三大发展方向为低成本化。目前采用PAN基碳纤维的成本较高,尽管通过提高产量可降低其成本,但仍达不到大多数工业和民用领域能接受的价格。在整个碳纤维的制备过程中,PAN原丝的成本约占总成本的50%,因此寻求廉价的原料替代PAN可大幅降低其成本。美国ORNL在DOE的资助下已开始使用木质素采用熔融纺丝方法制备碳纤维,目前已得到性能较好的连续化纤维,有望在未来作为增强材料而应用于汽车领域。此外,预氧化及碳化工艺及设备的改进也可大幅度降低碳纤维的成本。
表2-3 PAN基碳纤维的主要发展历程

2.4.3 我国碳纤维产业发展现状及趋势
我国碳纤维的研究始于20世纪60年代,但由于碳纤维作为重要的军工产品,国外对我国进行了严格的技术封锁,致使我国碳纤维技术基本以自主研发为主,进展缓慢,没能实现大规模的工业化生产。表2-4所示为我国碳纤维的主要发展历程。目前T300级碳纤维的工艺基本成熟,在一定程度上替代了进口碳纤维,同时T700和T800级碳纤维技术也取得了新的突破。2011年以来,我国多家企业可稳定生产T700级碳纤维,中复神鹰成为全球第三家采用干喷湿纺工艺生产T700的企业。2012年我国建成了首条T800级碳纤维生产线,并实现了稳定批量生产,目前已启动千吨级T800级碳纤维生产线的建设。
表2-4 我国碳纤维的主要发展历程

2016年,我国内地碳纤维制造商超过30家,24家具有工程产能以上产能的企业的理论产能为23810t,其中仅江苏恒神和中复神鹰的年产能超过4000t,一些企业的碳纤维生产设施甚至处于停运状态。表2-5所示为2016年我国碳纤维的主要生产厂家及对应的产能,其中台塑集团产能为8800t,为世界第六大碳纤维供应公司。中复神鹰和江苏恒神的产能分别为5000t和4660t,为国产碳纤维主要的生产厂商。在碳纤维项目方面我国也进行了大量的投资,蓝星威邦碳纤维项目一期投资10亿元,2013年投入试生产,项目全部达产后可生产碳纤维布50万m2,碳纤维材料230t;江苏航科投入2.5亿元,于2012年建成产能为25t/a的T800级碳纤维生产线,该公司于2014年2月成功研发出T1000级碳纤维;太原钢铁集团与山西煤化所合作共同开发高端碳纤维新材料,该项目投资6亿元,形成每年T800级碳纤维25t、M55J石墨纤维5t的产能,并于2014年进入试生产阶段[70]。
表2-5 2016年我国碳纤维的主要生产厂家及对应的产能

尽管我国近几年在碳纤维上的进步很大,但国内的碳纤维制造水平总体上落后于世界发达国家,主要表现在以下三个方面:①受产业化水平和制备技术的影响,国产碳纤维制备成本较高,影响其应用领域的拓展;②国产碳纤维品种偏少,质量稳定性差,难以完全满足市场应用要求;③国产碳纤维配套技术相对落后,若干装备关键技术仍未突破。因此我国碳纤维行业未来的发展方向主要包括原丝质量的提高、产品种类的增加、生产工艺的改进,关键设备的研发以及生产成本的降低。