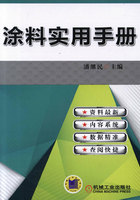
1.11 涂料的检测
1.11.1 涂料性能的检测
1.检测方法
常用的检测方法有:
1)GB/T 3186—2006《色漆、清漆和色漆与清漆用原材料取样》。
2)GB/T 1721—2008《清漆、清油及稀释剂外观和透明度测定法》。
3)GB/T 6750—2007《色漆和清漆 密度的测定 比重瓶法》。
4)GB/T 6753.3—1986《涂料贮存稳定性试验方法》。
5)GB/T 1723—1993《涂料粘度测定法》。
6)GB/T 1724—1979《涂料细度测定法》。
7)GB/T 1725—2007《色漆、清漆和塑料 不挥发物含量的测定》。
8)GB/T 1722—1992《清漆、清油及稀释剂颜色测定法》。
2.产品的取样
涂料在购进入库之前,应对其进行检查和验收,以避免在涂装过程中可能产生的质量事故、生产延误和经济损失。
涂料产品的检验取样极为重要,检验结果要具有代表性。其结果的可靠程度与取样的正确与否有一定的关系。国家标准GB/T 3186—2006规定了具体的取样方法。取样后由检验部门进行检验。
3.涂料外观检测
(1)目测涂料状态 观察涂料是否有结皮、胶凝、分层和沉淀等情况。
1)结皮是由于醇酸等类型的涂料氧化固化形成的。如果有结皮,则应沿容器内壁分离除去。结皮层已无法使用,下层涂料可继续使用,使用时需搅拌均匀。
除去结皮的涂料要尽快用完,以避免放置一段时间后结皮的再次产生,甚至报废。
2)如果色漆和清漆中出现了胶凝现象,可通过搅拌或加溶剂搅拌来除去,用时过滤。若不能分散成正常状态,则应报废。
3)涂料经长期存放,可能会出现分层现象,即溶剂和树脂浮于上层,颜料沉淀在下层。
其检测方法是用一棒形物插进涂料桶,若可插至底,则说明沉淀是松散的,可混匀后再使用。
采用搅拌器使涂料样品充分混匀。混匀的技巧是,先倒出部分上层溶剂,搅拌下层颜料和填料及树脂液,待初步分散均匀后,再把倒出的溶剂倒回,继续搅拌均匀。用时过滤。
4)若上述方法中的棒形物无法插到桶底,则说明沉淀时间过久,已干硬。可先把能流动的部分倒出,用刮铲从容器底部铲起沉淀,研碎后再把倒出的部分倒回原先桶中,充分混合。如果按此法操作无法混合,仍有干结沉淀,则涂料只能报废。
有条件的使用者,可按照GB/T 6753.3—1986来测定涂料的贮存稳定性。
(2)颜色 通常是用肉眼观察色漆的颜色,可与生产厂家提供的标准色板进行计较,色漆应符合指定的色差范围。
有条件的使用者,可按照GB/T 1722—1992来测定清漆、清油及稀释剂的颜色,用铁钴比色计目视比色进行测定。
(3)外观 通过目测观察涂料有无分层、发浑、变稠、胶化、返粗及严重沉降现象。
4.涂料黏度的测定
涂料的黏度又叫涂料的稠度,是指流体本身存在的黏着力阻碍流体流动的一种特性,即液体流动的阻力。
通过测定黏度,可以观察涂料贮存一段时间后的聚合度。可按照不同的施工要求,用适合的稀释剂调整黏度,以达到刷涂、有气和无气喷涂所需的不同黏度指标。
这项指标主要用于控制涂料的黏度,以使之合乎使用要求。涂料的黏度对其施工性能、涂膜的流平性和流挂性有直接的影响。
国家标准GB/T 1723—1993规定了3种测定黏度的方法,包括涂-1、涂-4黏度杯及落球黏度计测定涂料黏度的方法,其中最常用的测定方法是涂-4黏度杯测定法。
其测定方法是:在规定的温度下(如25℃),对搅拌均匀的原涂料液用涂-4杯测定涂料自杯中呈线状流出所需的时间。
基本要求是:杯子容积为100mL,测试时黏度计应该保持水平,涂料液面与杯口边缘齐平(用玻璃棒刮平);黏度计每次用后都应用溶剂洗净擦干才能进行下一个试样的测试。
操作注意事项:
1)测定的规定温度应在21~25℃之间,因为温度过高,测定的黏度比较低,而温度过低,测定的黏度又比较高,都不是标准值。
2)先用手指或器具堵住小孔漏嘴,倒满100mL涂料,用玻璃棒将气泡和多余试样倒入凹槽,确保试样为100mL。
3)迅速移开手指,同时开启秒表,待试样流束刚中断时立即停止秒表,计时。
4)每次测完都要清洁涂-4杯。选用与所测涂料相应的溶剂,以防止测定小孔被堵。
5.涂料细度的测定
涂料的细度是指涂料中所含颜料在涂料中分散的均匀程度,以微米表示。
涂料细度的优劣直接影响涂膜的光泽、透水性及贮存稳定性。
细度的测定按国家标准GB/T 1724—1979,采用刮板细度计来进行。
基本方法是:取几滴涂料滴在沟槽的最深端,持刮刀与平板垂直,自深槽部位向浅槽部位快速拉过(≤3s),使涂料充满平板沟槽,在5s以内以与沟槽表面呈15°~30°的视线角对光观察显露颗粒,记下相应的刻度线。在读数以上的相邻分度线内,不得超过3个颗粒。
细度读数法如图1-3所示。
各类涂料的细度要求如下:高装饰面漆15~20μm;平光面漆30~40μm;半光面漆25~35μm;防锈底漆不大于50μm。
细度不合格的产品,很多是因颜料研磨不细、外界杂质进入及颜料返粗等情况所造成,可返厂再经过滤、研磨,或降级使用。
图1-3 细度读数法
6.涂料固体分的测定
涂料的固体分也称涂料的固体含量,是指涂料组分中不挥发成分的含量。
涂料固体分直接影响到涂膜的丰满度和经济效益。涂料固体分越高,在涂装时成膜厚度就越高,故可节约大量的稀释剂,减少涂装道数,从而节约涂装经费,缩短施工时间,因此具有更大的经济效益。
测定常用溶剂型涂料固体分的方法可按照国家标准GB/T 1725—2007。
测定方法:将涂料试样称量后在一定温度下放入烘箱保温,干燥后再称量。剩余物质量与试样质量的比值,即为固体分(以百分数表示)。
操作注意事项:
1)称量用平底器皿需先恒重,不能有溶剂和水。涂料应均匀流平分布在器皿底部,不能过多或过少,一般称取2g左右,黏度较低的取样4g左右。
2)用红外灯法温度较高,升温速度快,测定过程短,但温度难以控制;用烘箱法测定时,可采用比红外灯法较低的温度。对因温度高而易分解的产品以采用烘箱法为宜。测定不同品种涂料固体分时的烘干规范温度见表1-29。
表1-29 测定不同品种固体分时的烘干规范温度
3)涂料试样在规定温度烘干(干燥要实干)后,取出在室温中冷却,称量一次;再次放入烘箱半小时后再称量,前后质量基本无变化(质量差不大于0.01g为止)即可。
4)箱中温度分布均匀,可同时进行较多数量的平行实验。有条件一般采用烘箱加热。
5)计算方法 涂料固体分X(%)按以下公式计算:
式中m0——容器质量(g);
m1——试样和容器质量(g);
m2——剩余物和容器质量(g)。
实验结果应取两次平行试验的平均值,且两次平行试验结果的相对误差不大于3%。
6)各类涂料产品的固体含量及兑稀到施工黏度时的稀释率,见表1-30。
表1-30 各类涂料产品的固体含量及稀释率
(续)
1.11.2 涂料施工性能的检测
涂装过程中的质量检测,对于控制涂装质量、节约涂装经费,以及得到高品质的涂装产品具有十分重要的意义。
1.检测方法
1)GB/T 1727—1992《漆膜一般制备法》。
2)GB/T 1726—1979《涂料遮盖力测定法》。
3)GB/T 9264—2012《色漆和清漆抗流挂性评定》。
4)GB/T 1728—1979《漆膜、腻子膜干燥时间测定法》。
5)GB/T 1762—1980《漆膜回粘性测定法》。
2.标准涂料试板的制备
国家标准GB/T 1727—1992规定了制备一般漆膜的材料、底板的表面处理、制板方法、漆膜的干燥和状态调节、恒温恒湿条件以及漆膜厚度等,适用于测定漆膜一般性能用试板的制备。
按GB/T 1727—1992制备的涂料样板,要进行有关漆膜性能的一系列检测工作,如测附着力、柔韧性、冲击强度等,因此所成漆膜的干膜厚度不应太厚,以10~80μm为宜,否则影响其他项目的测试性能。
除另有规定外,各种漆膜干燥后的漆膜厚度规定见表1-31。
表1-31 各种漆膜干燥后的漆膜厚度规定
(续)
3.涂料使用量的测定
涂料的使用量是指在单位面积底板上制成一定厚度的涂膜时所需的涂料量,以g/m2表示,也叫用漆量。
其测定方法分刷涂法和喷涂法,制板方法按上述介绍的涂膜的一般制备方法进行。
(1)刷涂法 基本原理:涂装前漆刷及盛有试样容器重,减去涂装后漆刷及盛剩余试样容器重,此差值除以涂装面积即可得到涂料使用量。
涂料使用量X(g/m2)按下式计算:
式中W1——涂装前漆刷及盛有试样容器重(g);
W2——涂装后漆刷及盛剩余试样容器重(g);
S——涂装面积(cm2)。
(2)喷涂方法 基本原理:称量喷涂前后试板的质量差值,再除以喷涂涂料的面积即可得到涂料使用量。
涂料使用量X(g/m2)按下式计算:
式中B——涂装后板重(g);
A——涂装前板重(g);
C——涂装面积(cm2)。
计算出涂料的使用量,再确知预涂装物体的表面积及共需涂装的道数,就可估计出工程所需购买的涂料的总重量(注意应考虑施工过程中的损耗)。
其计算公式为
涂料总重量=涂装物表面积×涂料使用量×涂装道数×损耗系数其中,损耗参数>1,在1.1~2.0之间,与被涂物形状、采用的涂装方法和施工气候条件等有很大关系。
4.涂料遮盖力的测定
遮盖力是指色漆均匀地涂在物体表面上,遮盖住被涂基体表面底色的能力。测定遮盖力多采用黑白格试验,以单位面积遮盖底色的最小涂料用量表示(g/m2)。
涂料的遮盖力与颜料颗粒的大小和它在涂料中的分散性有密切联系。不同种类的涂料由于颜色深浅、颗粒粗细、密度、折射率等不同,其遮盖力也不同。
国家标准GB/T 1726—1979规定了刷涂法和喷涂法两种测定遮盖力的方法。
(1)刷涂法 刷涂法的基本内容是采用按照标准规定黏度的涂料,用漆刷将涂料均匀地涂刷于黑白格玻璃板(10cm×20cm)上,在散射光下或在规定的光源设备内进行观察,至刚好看不见黑白格为止,用减量法求得黑白格板面积的涂料用量,再计算出涂料的遮盖力。
(2)喷涂法 喷涂法的基本内容是用喷枪将适当黏度的涂料喷涂于黑白格玻璃板上,目测至看不见黑白格为止,待涂膜成干膜后剥下称其重量,计算出涂料的遮盖力(以干膜计)。
5.涂膜厚度的测定
涂膜厚度分为湿膜厚度和干膜厚度。湿膜厚度用于施工现场对涂膜厚度的直接控制和调整,干膜厚度则用于质量监控与验收。
涂膜厚度是涂料施工过程中很重要的一项控制指标。涂装产品根据其用途和使用环境状况,对涂膜厚度有直接的要求。涂膜的各项性能也必须以厚度作为条件参数,即涂膜性能只有在同等厚度下才有可比性。
在涂装工程中,涂膜厚度是控制涂装质量的重要手段之一,以测量干膜厚度来确保工程涂装质量的方法叫膜厚管理。
涂膜厚度与涂装过程中出现的各种因素有关,如施工方式、施工时的不挥发分、底材的表面处理及吸附能力,以及稀释剂的挥发速度等。
涂膜厚度的控制有以下两种方法:
(1)湿膜厚度的测定 用带有深浅依次变化锯齿的金属板或圆盘垂直压在湿膜表面,直接读取首先沾有湿膜的锯齿刻度。
湿膜厚度未达到规定要求时,应通过补涂或局部修补后重涂来达到规定的厚度。
(2)干膜厚度的测定 常用的有杠杆千分尺测定和磁性测厚仪测定两种方法。随着涂料检测水平的提高,一般多采用磁性测厚仪法。
磁性测厚仪法的操作步骤是,将探头放在样板上,使之与被测涂膜完全吸合,指针(数字式旋钮)随着测定膜厚值的不断变化,当磁芯跳开、表针数字稳定时,即可读出涂膜厚度值(以μm表示)。
操作测厚仪时需注意以下事项:
1)干膜测厚仪在每天使用前、后要进行校正,在使用过程中若发现仪表的精确度下降或异常,应及时校正。
校正方法:校正时将探头直接置于基体上,将相应的旋扭旋到“0”位,以校正0点;将仪器带有的标准膜厚的校正片置于基体上,调整相应的旋扭,使表针(标尺)的读数等于标准膜片的厚度;重复此操作,直至调到“0”位和适当的厚度为止。
2)干膜厚度的测量要求涂膜必须实干且干透,若探头按压在涂膜表面留有印记,则说明涂层未干透,坚硬程度不够,此时的测试必定会有误差。
3)检验涂层的各项物理指标或统计整个施工完毕的涂膜总厚度均以测干膜为准,如果总干膜达不到规定厚度,则不能起到相应的防腐保护作用,因此必须根据实际情况补涂一至二道涂料。
4)在实际操作时,不能为了追求高的膜厚而一次涂装的过厚,以免出现流挂、起皱、桔皮等弊病。
6.涂料流平性的测定
涂料的流平性又称为展平性或匀饰性,它是衡量涂料装饰性能的一项重要指标。
1)一种测定涂料流平性的经验方法是,刷涂时自刷子离开样板的同时开启秒表,测定刷子划过的刷痕消失和形成完全平滑涂膜表面所需的时间,以min表示。若采用喷涂法,则观察涂膜表面达到均匀、光滑、无皱状态所需的时间。
2)另一种测定涂料流平性的经验方法是,将涂料试样调至施工黏度,涂刷在已有底漆的样板上,使之平滑均匀,然后在涂膜中部用刷子纵向抹一刷痕,观察刷痕消失、涂膜又恢复成平滑表面的时间。
涂料流平性的评级标准一般按照涂膜达到均匀平滑表面的时间来评级:不超过10min者为良好,10~15min为合格,超过15min者为不合格(非装饰性涂层可不作此要求)。
涂料流平性的优劣与涂料的品种和黏度有极大的关系,黏度大的涂料一般流平性不如低黏度的涂料。随着科技的发展,近年来,许多新型流平助剂逐步得到应用,如聚丙烯酸酯类流平剂,只需加入0.2%~1.0%(质量分数)的用量,就能大大提高涂膜的整体流变性和流平性。
7.涂料抗流挂性的测定
由于被涂布在垂直表面上的涂料流动不适当,使涂膜产生不均一的条纹和流痕就是流挂现象。它反映在施工上,抗流挂性就是涂料在干燥过程中不会产生流动趋势的最大湿膜厚度。
涂料的流挂性是测定厚浆(厚膜型)涂料最重要的指标。
国家标准GB/T 9264—2012规定了测定色漆相对流挂性的方法。
测定涂料流挂性的操作步骤如下:①首先,将玻璃板放在底座的适宜位置上,并将刮涂器置于试板面顶端,刻度朝向操作者。②将足量充分搅匀的样品均匀倒在刮涂器前面的开口处。③两手握住刮涂器两端,使其平稳连续地从上到下进行刮拉,同时应保持平直而无起伏,在2~3s内完成这一操作。④将刮完涂膜的试板立即垂直放置。⑤观察读数时检查流挂情况,若该条厚度涂膜不流到下一个厚度条膜内,即分界线清晰,则此条膜的厚度为不流挂的湿度厚度,以μm计。
操作注意事项:
1)注意双组分涂料应搅拌均匀且有一定的活化期和使用期效,单组分涂料不能让溶剂过度挥发。
2)注意放置涂膜试板时,应使条膜呈横向且保持“上薄下厚”,即将试板横向且刻度小的条膜放于上端。
3)由于刮涂的原因,涂膜两端各20mm内的区域不计,观察条膜中段的分界线。
抗流挂性的测定可用于判断一次成膜涂料的干膜厚度和用量。
8.涂膜干燥时间的测定
涂膜干燥时间是指涂料以一定厚度涂装在物体表面上,经过物理性挥发或化学性氧化聚合作用,或采用添加固化剂、烘干或光固化等方法,形成固体薄膜的过程所需要的时间,以h或min表示。
涂膜的干燥时间取决于涂料本身的化学性能和物理性能,通常可分为表面干燥和实际干燥两个阶段。
1)表面干燥,即一定厚度的湿膜的表面从液态变为固态但其下仍为液态,其干燥时间称表干时间。
2)实际干燥,即施涂好的一定厚度的涂膜从液态变成固态,其干燥时间称为实干时间。
漆膜、腻子膜干燥时间的测定方法可参照国家标准GB/T 1728—1979的具体内容。
(1)表干时间的测定 主要有吹棉球法和指触法,这种测试主要凭测试者的经验。
1)吹棉球法是在涂膜表面轻轻放一棉球,然后用嘴轻吹棉球,如果能吹走且涂膜表面不留有棉纤维,即认为表干。
2)指触法是以手指轻触涂膜表面,如果感到有些发黏,但不粘手指,也无漆粘在手指上,即认为表面干燥(简称表干)。
(2)测定实干的方法 有压滤纸法、压棉球法和刀片法等。
1)压滤纸法是在涂膜表面放一滤纸,再压上干燥试验器(200g的砝码型),30s后移去砝码,然后将试板翻转,若滤纸能自由落下且纤维不粘在涂膜上,或者用手指在背面轻敲几下,有一两根纤维黏附但也能轻轻掸掉,则认为涂膜实干。从涂料涂刷到此时的时间即为所要测定的实干时间。
2)压棉球法是在涂膜上放一个脱脂棉球,于棉球上再轻轻放上干燥实验器,同时开启秒表,经30s后,将干燥实验器和棉球拿掉,样板转动5min,观察涂膜有无棉球的痕迹及失光现象,涂膜上若留有一两根棉纤维,用手指能轻轻掸掉,则认为涂膜已实际干燥。从涂料涂刷到此时的时间即为所要测定的实干时间。
9.涂料打磨性的测定
打磨性一般是以砂纸打磨时的粘砂性或打磨平整的难易程度来判断。
在涂装作业过程中,总是需要对工件进行局部的打磨修整,对于在旧涂膜表面或腻子表面涂装,还需要进行彻底的整体打磨。
打磨是涂装过程中必不可少的一道工序,打磨的难易程度对施工效率有直接影响。
若粘砂严重,打磨时感觉发腻,打磨平整就不太容易,打磨性就差。
涂料打磨性的测定方法可参照国家标准GB/T 1770—2008的具体内容。
通常来说,硬涂膜有较好的打磨性,软涂膜的打磨性很差。
10.涂料重涂性的测定
重涂性是指在规定间隔时间内,涂膜表面用同一涂料进行再次涂覆的难易程度及涂覆效果的好坏。
因此,复合涂层体系或多道涂覆时,重涂性就表现为一项非常重要的施工性能。当然,重涂性是可以通过对施工工艺条件的调整来改善的。