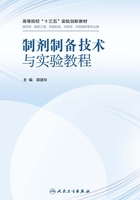
上QQ阅读APP看书,第一时间看更新
第六节 无菌生产工艺技术
一、无菌生产工艺技术的应用特点
无菌操作法系指整个过程控制在无菌条件下进行的一种操作方法。操作中所用的一切原料、辅料、用具及操作空间都要预先灭菌,对操作人员的卫生有严格的要求,操作应在A级洁净室中进行。
该法适合一些不耐热药物的注射剂、眼用制剂、皮试液、海绵剂和创伤制剂的制备。按无菌操作法制备的产品,一般不再灭菌,但某些特殊(耐热)品种亦可进行再灭菌(如青霉素等)。
1.无菌操作室的灭菌
常采用紫外线、液体和气体灭菌法对无菌操作室环境进行灭菌。
(1)甲醛溶液加热熏蒸法:
该方法的灭菌较彻底,是常用的方法之一。气体发生装置是采用蒸汽加热夹层锅,使液态甲醛汽化成甲醛蒸气,经蒸气出口送入总进风道,由鼓风机吹入无菌室,连续3小时后,关闭密熏12~24小时,并应保持室内湿度>60%,温度>25℃,以免低温导致甲醛蒸气聚合而附着于冷表面,从而降低空气中甲醛浓度,影响灭菌效率。密熏完毕后,将25%的氨水经加热,按一定流量送入无菌室内,以清除甲醛蒸气,然后开启排风设备,并通入无菌空气直至室内排尽甲醛。
(2)紫外线灭菌:
是无菌室灭菌的常规方法,该方法应用于间歇和连续操作过程中。一般在每天工作前开启紫外灯1小时左右,操作间歇中亦应开启0.5~1小时,必要时可在操作过程中开启。
(3)液体灭菌:
是无菌室较常用的辅助灭菌方法,主要采用2%煤酚皂溶液、0.2%苯扎溴铵或75%乙醇喷洒或擦拭,用于无菌室的空间、墙壁、地面、用具等方面的灭菌。
2.无菌操作
无菌操作室和层流洁净工作台是无菌操作的主要场所,无菌操作所用的一切物品、器具及环境,均需按前述灭菌法灭菌,如安瓿应150~180℃、2~3小时干热灭菌,橡皮塞应121℃、1小时热压灭菌等。操作人员进入无菌操作室前应洗澡,并更换已灭菌的工作服和清洁的鞋子,不得外露头发和内衣,以免污染。
小量无菌制剂的制备,普遍采用层流洁净工作台进行无菌操作,该设备具有良好的无菌环境,使用方便,效果可靠。
二、无菌生产工艺技术的应用关键问题
1.无菌制造系统中工艺平面布置应遵循的原则
无菌制造系统在生产工艺上,应对使用的洁净厂房特别加以布置设计,尤其是应着重考虑洁净工房工艺平面对无菌制造的适用性和可靠性。无论是进行无菌的粉末分装还是无菌的液体分装,都应着重解决工艺平面布置对无菌制造工艺过程的无菌保证度。
2.无菌制造对工房装修及材料的要求
无菌制造系统使用工房的装修,应体现出工房围护结构的空气密封性好,房内无卫生死角,装修材料表面光洁但不反光、耐压力而不起尘、易于清洁、不易发生霉变和长菌、能够适应各种消毒剂和气体灭菌熏蒸的腐蚀和紫外线照射。
3.无菌制造对生产设备的特殊要求
无菌制造工艺对生产设备的要求,主要围绕参与无菌制造的设备会不会对制品产生污染或降低制造系统的无菌保证程度加以考虑。与无菌药品、包装容器和密封零件相接触的设备表面也应是无菌的。为了满足设备的表面处于无菌状态,要求设备的材料能够耐受高温蒸汽或化学气体的消毒处理,而且有可能灭菌蒸汽按照工艺要求使用的是纯蒸汽。由于纯蒸汽对不锈钢材料的晶间会产生腐蚀,设备可能需要用抗晶间腐蚀能力较强的材料(如316L)来制造。另外,在无菌制造工艺中,参与无菌制造的设备表面灭菌工艺的验证与药品、容器和密封零件灭菌工艺的验证处于同等重要的地位。假如灌装设备、连接管道以及过滤器支架等设备使用蒸汽灭菌法消毒处理,则湿热灭菌设备中灭菌物装载方式的确定就很重要,因为不同的装载方式会影响灭菌设备内部的热分布情况和实际的灭菌效果。通常,除了正常生产状态下的装载方式应进行灭菌效果试验以外,还应进行最大和最小装载条件的灭菌效果试验。
4.无菌制造对工艺用水的要求
使用无菌制造工艺生产的药品大多数为注射用产品,也有非注射剂如滴眼剂。注射用产品需要考虑热原,因而应采用注射用水。注射用水用于配制产品,以及最终洗涤生产中所用的器件和设备。注射用水需极高的纯度、不含内毒素,注射用水规定的合格工作极限为10CFU/100ml。由于抽样检测的局限性,通常,注射用水的品质从水的制备、贮存、分配系统和水系统的微生物控制这4个方面的情况加以评价。
5.无菌制造对空调净化的要求
在无菌制造工艺过程中,灭过菌的产品、容器和密封件所暴露的环境区域应特别留意。该区域内的作业活动包括灌装前和灌装封口过程中对这些无菌物料和产品的操作处理,其操作通常是在无菌操作区内中进行的。因为在这个区域内产品处于开口状态,极易受到污染,且产品灌装封口后也不再作进一步的灭菌处理。为了保证产品质量,特别是无菌指标,无菌操作应在最优质量的环境中进行,其是由空调净化系统来实现的。无菌制造环境评价的主要内容之一是空气的质量,主要是制造环境中空气的悬浮粒子含量。空气中悬浮粒子因其可能进入产品造成污染显得非常重要。另一方面,空气中悬浮粒子可能作为微生物的载体,污染制造过程中的无菌产品。因此,减少空气中悬浮粒子的含量和有效地去除已存在的固体微粒子,始终都是制造过程控制的主要内容。大面积的无菌区域内空气的洁净度至少应为B级,此洁净度下的每立方米空气中含有粒径≥0.5µm的粒子数应不得超过350 000个,空气中浮游菌的含量应不得超过100CFU/m 3。无菌容器和密封件以及灌装封口作业的局部暴露区域内空气的洁净度应达到A级要求,该洁净度下每立方米空气中含有粒径≥0.5µm的粒子数应不得过3500个,空气浮游菌的含量应不得超过5CFU/m 3。无菌操作区域内的A级洁净区内的空气在其使用点处应经高效过滤器过滤后呈单向流态(层流)输送,流速应满足空气以活塞的方式吹除灌封区内的悬浮粒子的需要。按规定,垂直单向流的气流速度为3.5m/s±20%,水平单向流的气流速度为4.5m/s±20%。但是,如果制造工艺的操作过程中可能会产生大量粒子或设备的几何形状会干扰层流状的空气流态,则需要设计使用。
6.无菌制造对工业气体的要求
在无菌制造的操作区内还要使用的其他气体,其固体微粒子和微生物同样应具有高度的质量。与产品、容器和密封件或产品接触表面相接触的其他气体(例如用于净化和保护目的的气体)均应经过除菌过滤处理。此外,在无菌区域内使用的压缩空气中也不得含有油或油的蒸气成分。
7.无菌制造对环境卫生的要求
无菌制造系统的操作区域还需要对围护结构的墙面、地面、天花板、门窗等环境设施进行卫生处理。通常要求使用多种清洁剂对制造环境进行适当的消毒和灭菌,常用清洁剂有以下3类:
(1)作为清洗和强烈的杀菌剂(如胺盐与非离子表面活性剂)。
(2)作为清洗和不含杀菌剂(非离子表面活性剂,无机螯合剂)。
(3)作为清洗窗户的清洁剂。
这3类清洁剂根据无菌操作区域的不同需要清洁地面时,清洁剂应交替使用。
8.无菌制造对人员的要求
只有经过批准、经过专门培训的人员方可进入无菌操作区内,无论何时均需遵守这个原则。例如非无菌操作区的人员和外来参观者需进入该操作区时,必须经过有关部门批准。