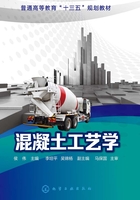
第1章 绪论
1.1 混凝土发展概况及趋势
1.1.1 混凝土发展概况
早在公元前,古罗马人就利用石灰与火山灰混合料浆加入石渣、砖块、天然卵石等制成混凝土。利用这种混凝土建成的各种建筑,如著名的万神庙、古罗马竞技场等已有2000年左右的历史,其整体结构或主要部分至今依然完好。我国也有利用石灰与火山灰筑造的部分长城和城墙,而且进一步利用人造火山灰——烧黏土或红砖粉拌合石灰,在明代和清代建成各种储水和输水建筑,其功效也历经考验。不同的是古罗马火山灰本身含有约10%的Na2O和K2O(与石灰混合后实质就是最原始的碱激发水泥),我国和世界上大多数国家的火山灰含Na2O和K2O较少。因此,世界上大多数石灰火山灰混凝土,凝结硬化较慢、早期强度较低。随着历史的发展,石灰火山灰胶凝材料逐步被天然水泥和波特兰水泥所取代。对比混凝土所用胶凝材料种类的变化过程,可发现其实质上是矿物组成由基本独立的活性CaO、SiO2和Al2O3矿物体系向合成的活性硅铝酸钙矿物体系的转变,也是其化学成分当中CaO含量与SiO2+Al2O3含量之比大体上由低向高的转变。因而使混凝土具有更优良的工作性、凝结时间和早期强度。
1824年英国工程师约瑟夫·阿斯普丁(Joseph AsPdih)获得第一份水泥专利,标志着水泥的发明。这以后,水泥以及混凝土才开始广泛应用到建筑上。19世纪中叶,法国人约瑟夫·莫尼哀(1823—1906)制造出钢筋混凝土花盆,并在1867年获得了专利权。在1867年巴黎世界博览会上,莫尼哀展出了钢筋混凝土制作的花盆、枕木,另一名法国人兰特姆展出了钢筋混凝土制造的小瓶、小船。1928年,美国人Freyssinet发明了一种新型钢筋混凝土结构形式:预应力钢筋混凝土,并于二次世界大战后被广泛地应用于工程实践。钢筋混凝土和预应力钢筋混凝土解决了混凝土抗压强度高,抗折、抗拉强度较低的问题,使高层建筑与大跨度桥梁的建造成为可能。
19世纪中后期,清朝洋务派进步人士掀起学习西方先进工业技术的高潮,并在上海建成了我国第一家水泥厂,当时,称水泥为“洋灰”。在19世纪末20世纪初,我国也开始有了钢筋混凝土建筑物,如上海市的外滩、广州市的沙面等,但工程规模很小,建筑数量也很少。1949年以后,我国在落后的国民经济基础上进行了大规模的社会主义建设。随着工程建设的发展及国家进一步的改革开放,混凝土结构在我国各项工程建设中得到迅速的发展和广泛的应用。
早期混凝土组分简单(水泥、砂、石子、水),强度等级低,施工劳动强度巨大,靠人工搅拌或小型自落式搅拌机搅拌,施工速度慢,质量控制粗糙。高性能混凝土外加剂的广泛应用,是混凝土发展史上又一座里程碑。外加剂不但可以减少用水量、实现大流动性,还能够使混凝土施工变得省力、省时、经济。
20世纪30年代末,美国发明了松脂类引气剂和纸浆废液减水剂,使混凝土的耐久性以及和易性得到前所未有的提高。20世纪60年代,日本和德国相继成功研制出了萘系高效减水剂和三聚氰胺树脂系高效减水剂。在相同水胶比的条件下,掺入高效减水剂可以使混凝土的坍落度成倍提高,即使是水胶比很低的高性能混凝土,坍落度仍能达到200~250mm。其实,在混凝土中掺入外加剂的做法并非现代才有,罗马建筑告诉我们,当时的混凝土中经常加入动物血或鸡蛋白,来改善混凝土的工作性和耐久性。唐宋以来用桐油、糯米汁、牛马血、杨桃藤汁掺入石灰砂浆中提高防水与耐久性。近代的各种增强混凝土,掺加混合材与各种外加剂,都是用来改善混凝土性能,以达到增强、耐久、经济等目的。
20世纪末期,出现了集中搅拌的专业混凝土企业,使泵送混凝土施工中混凝土的搅拌供料有了保证。1978年,在江苏省常州市,中国建成第一家混凝土搅拌站,当时每盘混凝土只能搅拌1m3。十一届三中全会后,我国确立了经济改革开放的基本国策,城市建设突飞猛进,混凝土搅拌站在沿海地区如雨后春笋般大量涌现。
跨入21世纪,计算机技术、机械工业技术、先进检测分析研究技术、现代管理技术的飞速进步,我国预拌混凝土技术的发展与时俱进,取得了世界瞩目的成就。天津117大厦其混凝土泵送高度达621m,创下混凝土泵送高度吉尼斯世界纪录。天津117大厦的建造成为中国乃至世界的又一标志性建筑,从混凝土实际泵送高度上,621m的泵送高度一举超越了迪拜哈利法塔601m的“净身高”,同时也超越了上海中心大厦606m的混凝土泵送高度,创造了世界混凝土泵送第一高度。
目前一些发达国家,如日本、美、英等许多国家已基本在全部混凝土中掺用外加剂,其中必掺的外加剂是引气剂,只有在少数的特种混凝土中才不掺引气剂。我国在20世纪50年代就开始使用外加剂,在70年代中期,又掀起了使用和研制外加剂的热潮,但与国外发达国家相比仍存在很大差距。尤其是引气剂的使用情况,目前与发达国家的使用情况几乎相反,只在少数的混凝土中掺用了引气剂。
20世纪50年代,国际上将高强混凝土定义为抗压强度35MPa及以上,70年代为50MPa及以上,80年代为60MPa及以上,90年代为80MPa及以上。我国《普通混凝土配合比设计规程》(JGJ 55—2011)和《建筑材料术语标准》(JGJ/T 191—2009)将高强混凝土定义为:强度等级不低于C60的混凝土。我国天津117大厦,其中混凝土最高强度等级达到C120。现在人们已经能够配制150MPa的混凝土;配制200MPa的活性粉末混凝土(掺入纤维,去除粗骨料,增大堆积密度和匀质性)。活性粉末混凝土在薄壁钢管的约束下,抗压强度可提高至375MPa;使用金属粉末取代砂子时,混凝土的抗压强度甚至可达800MPa。
然而,在混凝土强度不断提高的进程中,混凝土的耐久性并非全部得到了提高,其中甚至还有降低的情况。从20世纪70年代起,发达国家已有投入使用的诸多基础建设和重大工程出现了过早破坏的问题。如美国有25.3万座混凝土桥梁,桥面板使用不到20年就开始破裂。英国英格兰的中环城快车道上有8座高架桥,全长21km,总造价约2800万英镑,而2004年修补费用达1.2亿英镑。我国房屋与基础设施的使用年限低于世界平均水平,且远远达不到设计的要求。有的公路桥梁甚至仅使用3~5年就出现了破损现象,个别桥梁建成后尚未投入使用便开始维修,甚至边建边修,大大缩短了混凝土结构的服役寿命。其内在原因与水泥中C3S含量和粉磨细度的盲目提高以及混凝土水胶比的不适当变化都有必然的联系。
为提高混凝土的耐久性,1968年以来,日本、美国、加拿大、法国、德国等国家大力投入开发和研究高性能混凝土。1990年,美国国家标准与技术研究院(NIST)和ACI201委员会将其定名为“HPC”,它否定了过去过于偏重强度的发展道路,美国学者认为:HPC是一种易于浇筑、捣实、不离析,能长期保持高强度、高韧性和体积稳定性,在严酷条件下使用寿命很长的混凝土。我国学者及专家认为:高性能应体现在工程力学特性、新拌混凝土施工特性、使用寿命和节能利废(经济学特性)的综合能力之上。然而,在何种应用环境下何种结构的混凝土才具有最佳的技术经济性能,以及如何采用切实可行的手段使各种混凝土具有相对的高性能,目前尚需不断深入的研究。
1.1.2 混凝土发展趋势
现代科技革命给混凝土的研究和发展带来巨大的冲击和挑战,同时也带来了机遇和促进。随着混凝土朝着高性能、智能和绿色化的方向不断发展,随着人类社会经济的高速发展,基础设施建设的不断加快,人民生活水平逐渐提高而对住房的需求日益增大,混凝土材料必将以其经济、耐久、智能、绿色等特点成为建筑工程领域中使用最广泛的材料。
(1)高性能化
混凝土的高性能化主要体现在高工作性、高强度和高耐久性(水工混凝土的抗渗、寒冷地区的抗冻、机场和公路混凝土路面的抗冲耐磨、海工或化工混凝土工程的抗酸性侵蚀、大体积混凝土的抗裂等)几个方面。高工作性可通过复合超塑化剂来实现,使得混凝土能够无须振捣靠自重流平模板的每一个角落,即自密实混凝土。高强度可以通过复合各种纤维来实现,法国研究人员通过特殊工业复合直径0.15mm、长度13mm、最大体积掺量为2.5%的钢纤维,在400℃的养护条件下,制备出的超高强混凝土其抗压强度达到800MPa。这种混凝土在韩国得到了商业应用,如Cheong人行桥,跨度120m,拱高130m,其细长比创造了世界纪录。高的耐久性,根据不同要求复合不同的材料,如复合化学纤维、超细矿物掺合料或引气剂等可以提高混凝土的抗渗性和抗冻性,复合钢纤维和硅灰可以提高路面的抗冲耐磨性能,复合高炉矿渣和粉煤灰可以有效提高混凝土的抗硫酸盐侵蚀能力,复合大掺量粉煤和相变材料(如冰)可以减少大体积混凝土内部温升从而控制其开裂等。
(2)智能化
所谓智能化,就是在混凝土原有的组分的基础上复合智能型组分,使混凝土材料成为具有自感知、自记忆、自调节、自修复特性的多功能材料。自感知混凝土就是在混凝土基材中加入导电相可使混凝土具备本征自感应功能,例如在混凝土中加入具有温敏性的碳纤维,使得混凝土具有热电效应和电热效应。
日本学者研制了自动调节环境湿度的混凝土,该混凝土本身即可完成对室内环境湿度的探测,并根据需求对其进行调控。这种为混凝土材料带来自动调节环境湿度功能的关键组分是沸石粉,其作用机理为:沸石中的硅钙酸盐含有3×10-10~9×10-10m的孔隙,这些孔隙可以对水分、NOx和SOx气体选择性吸附,通过对沸石种类进行选择(天然的沸石有40多种),可以制备出符合实际需要的自动调节环境湿度的混凝土复合材料。它具有如下特点:优先吸附水分;水蒸气压低的地方,其吸湿容量大;吸放湿与温度相关,温度上升时放湿,温度下降时吸湿。这种材料已成功用于多家美术馆的室内墙壁,取得非常好的效果。
自修复混凝土是模仿动物的骨组织结构和受创伤后的再生、恢复机理,采用粘结材料和基材相复合的方法,对材料损伤破坏具有自行愈合和再生功能,恢复甚至提高材料性能的新型复合材料。日本学者将内含粘结剂的空心胶囊掺入混凝土材料中,一旦混凝土材料在外力作用下发生开裂,空心胶囊就会破裂而释放粘结剂,粘结剂流向开裂处,使之重新粘结起来,起到愈伤的效果。
(3)绿色环保化
混凝土虽然拥有众多优势,但其对环境的影响却不能忽视。混凝土每年大约消耗15亿吨的水泥和近90亿吨的天然砂石料,可以说是世界上最大的天然资源用户,其生产和应用必将给生态环境带来许多不利的影响。所以混凝土就必然面临这一问题所带来的冲击,可持续经济、循环经济、节能减排等一系列国家政策要求混凝土必须走绿色环保之路。
①以工业废料代替水泥 许多工业废料如煤热电厂排放的粉煤灰、炼钢厂排放的粒化高炉矿渣(磨细)、工业燃煤后留下的未能充分燃烧的煤矸石(磨细),生产硅金属时排放的硅灰等都可以用来部分代替水泥,而不降低混凝土的性能。事实上,这些工业废料等量代替水泥后,如果配料得当,往往能够提高混凝土的各种性能,如强度和耐久性能。我国的三峡大坝,使用2800万立方米混凝土,混凝土约6720万吨,其中的粉煤灰替代水泥的量为40%,既减少了成本,又成功解决了三峡大坝大体积混凝土温升的问题。硅灰已成为现代高强高性能混凝土必不可少的矿物掺合料之一。
②建筑垃圾循环利用 如果将占混凝土质量80%左右的天然骨料(砂、石)全部用工业和建筑垃圾代替,将具有重要意义。将工业和建筑垃圾(如拆迁的废砖和废旧混凝土)破碎后,经过分级、清洗和配比都可以制成再生骨料,再用其部分或全部代替天然骨料制成混凝土(再生混凝土),这种再生骨料的替代率越高,混凝土的绿色度自然就越高。香港理工大学的S.C.Kou等人将废旧混凝土破碎后制成再生粗细骨料,100%代替天然砂石,配制出28d强度为64.2MPa的高性能再生自密实混凝土。